Story
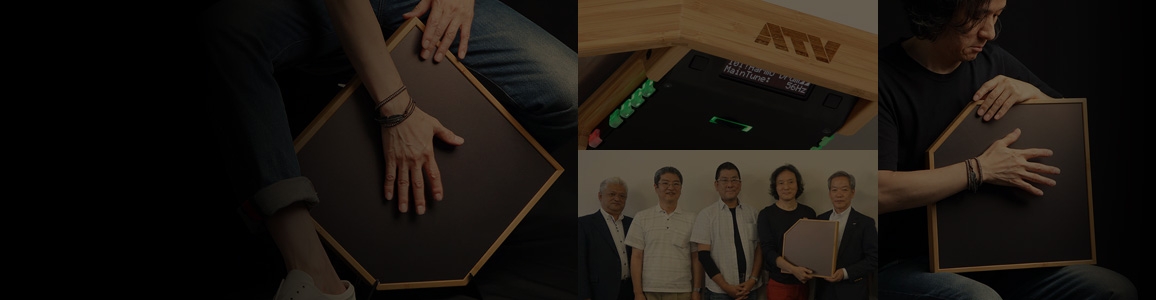
The contents of this page are reprinted with permission an article ICON.jp was interviewed and edited.
Product Development Story:
ATV aFrame--A Next-Generation Electric Instrument Created through a Fusion of an Acoustic Instrument, DSP Technologies, and Traditional Japanese Craftsmanship
ATV is an emerging instrument manufacturer founded by Ikutaro Kakehashi, a legend in the world of music instruments. ATV’s electronic drum “aD5,” the first product from ATV, has garnered a lot of attention for its high-definition sound performance, cutting-edge specifications, and divergence from the norm. ATV is now launching its new electrorganic percussion instrument known as the aFrame--a unique electronic instrument compatible with traditional percussion instrument playing techniques.
The diamond-shaped frame drum is equipped with high-performance built-in piezo-microphones, pressure sensors, and a strong DSP circuit. Sounds produced by the player’s bare hands are picked up, processed and output by the DSP based on ATV’s proprietary Adaptive Timbre Technology, an innovative technology that produces diverse tones by modifying the harmonic makeup of the signal input. This allows for compatibility with various playing techniques not supported by conventional electronic percussion instruments, which simply trigger PCM sound sources. Players can use traditional playing techniques such as striking, pressing, friction, and snapping the playing surface for expressive playing and phrasing. Of course there is no latency because the aFrame is not a mere combination of sound sources and pads. A player can freely play electronic sounds as if they’re playing an acoustic instrument.
The beautiful appearance--like that of a work of art--is another feature of the aFrame. The frame body, which has a decisive influence on output sound quality, is made of laminated bamboo. The frame is beautifully hand-crafted by experienced and skilled craftsmen of the renowned instrument workshop Fujigen. (Wow!)
Thus, the aFrame is a long-awaited next-generation electronic instrument produced by the legendary Ikutaro Kakehashi through the fusion of an acoustic instrument, DSP technologies, and traditional Japanese craftsmanship.
A reporter from ICON visited Matsumoto, the home of ATV’s development site and Fujigen’s plant, and interviewed the people involved in the development of the aFrame. The interviewees were Mr. Makoto Muroi, the President & CEO of ATV, Mr.Tsukasa Arakawa, the Producer at the R&D Dept. of ATV’s Matsumoto Laboratory, Mr. Tsutomu Tanaka, the mechanical engineer of the R&D Dept. and Mr. Ikuo Kakehashi, the aFrame development advisor and percussion performer. For the frame, we also interviewed Fujigen’s staff in charge of production.
The diamond-shaped frame drum is equipped with high-performance built-in piezo-microphones, pressure sensors, and a strong DSP circuit. Sounds produced by the player’s bare hands are picked up, processed and output by the DSP based on ATV’s proprietary Adaptive Timbre Technology, an innovative technology that produces diverse tones by modifying the harmonic makeup of the signal input. This allows for compatibility with various playing techniques not supported by conventional electronic percussion instruments, which simply trigger PCM sound sources. Players can use traditional playing techniques such as striking, pressing, friction, and snapping the playing surface for expressive playing and phrasing. Of course there is no latency because the aFrame is not a mere combination of sound sources and pads. A player can freely play electronic sounds as if they’re playing an acoustic instrument.
The beautiful appearance--like that of a work of art--is another feature of the aFrame. The frame body, which has a decisive influence on output sound quality, is made of laminated bamboo. The frame is beautifully hand-crafted by experienced and skilled craftsmen of the renowned instrument workshop Fujigen. (Wow!)
Thus, the aFrame is a long-awaited next-generation electronic instrument produced by the legendary Ikutaro Kakehashi through the fusion of an acoustic instrument, DSP technologies, and traditional Japanese craftsmanship.
A reporter from ICON visited Matsumoto, the home of ATV’s development site and Fujigen’s plant, and interviewed the people involved in the development of the aFrame. The interviewees were Mr. Makoto Muroi, the President & CEO of ATV, Mr.Tsukasa Arakawa, the Producer at the R&D Dept. of ATV’s Matsumoto Laboratory, Mr. Tsutomu Tanaka, the mechanical engineer of the R&D Dept. and Mr. Ikuo Kakehashi, the aFrame development advisor and percussion performer. For the frame, we also interviewed Fujigen’s staff in charge of production.
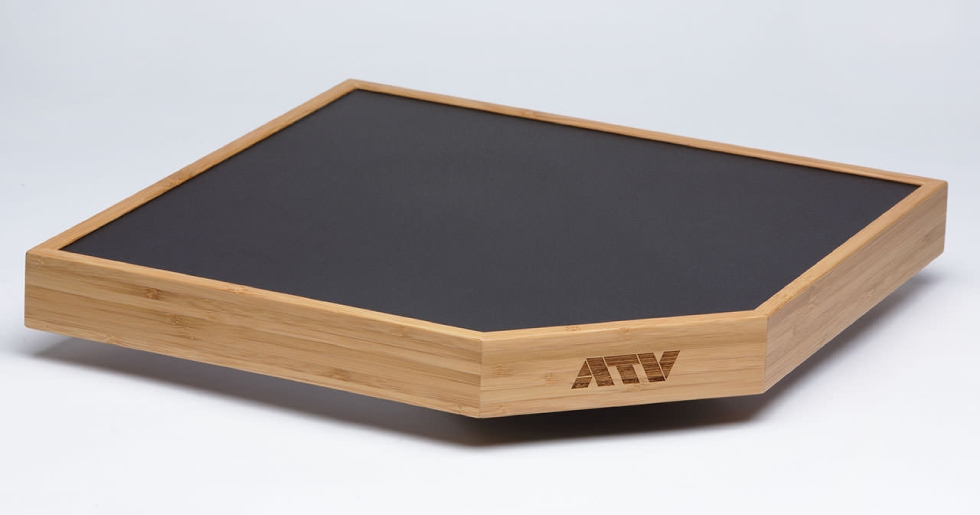
aFrame produces diverse sounds by modifying the impulse’s harmonic composition
——— The new aFrame is a very unique electronic instrument like nothing else. Where did the idea of picking sounds up by built-in microphones integrated in the diamond shaped frame and processing the sounds by DSP come from?
Muroi “To tell the truth, it was EQ, not an instrument, at the very beginning of the development. When we met to exchange various ideas, Ikutaro Kakehashi (Executive Chairman of ATV) suddenly said; ‘Isn’t it more interesting to process sounds picked up by microphones?’ That was actually the starting point of where the aFrame is now. I know he is a specialist in sound processing; even now he sometimes says that many more things could have been done for synthesizers through original sound processing at the time of analog-digital conversion! So, Arakawa took charge of further research on this 'something more interesting with sound processing' about two years ago.”
Arakawa “After that, I explored that 'something interesting,' which is accomplished by splitting the original sounds into spectra and using a filtering algorithm etc. Then, Mr. Ikutaro Kakehashi said to me, ‘Wouldn't it be great if we can have something like Timbre EQ that allows for a change in tone timbres just by operating a knob?’ That is not an EQ that can only change frequency, Q, and the gain of sounds, but an EQ that can also radically change the entire tone timbre. Well, I thought Timbre EQ was so interesting that we began a process of trial and error.”
——— By what algorithm did you try to make “Timbre EQ”?
Arakawa “After a variety of experiments, we noticed that modifying the harmonic makeup can produce interesting sounds; for instance, we superimposed even-harmonic overtones over odd-harmonic overtones. Of course we can’t add any sound component that doesn't exist in the original sound, but any subtlety found in original sound can be amplified. At first we tested by using simple waveforms such as rectangular and sawtooth waves, but these simple waveforms could be transformed into totally different waveforms by modifying the harmonic makeup. We found this interesting and decided to take our R&D efforts down this path.
Next we tested using a human voice as an input source, but the result was really boring! This was because with the human voice the pitch is constantly varying, so equalizing such sounds requires frequencies to follow such variations. However, the pitch has been changed once an input sound is detected. So, the output sounds were unimpressive. Also, with continuous sounds, such as the human voice, variations made by EQ are necessarily masked and the resultant sounds appear to have changed in frequency characteristics only. I presented the sounds to Mr. Ikutaro Kakehashi and as expected, he said ‘That’s no good!’ (Laughs) So, we thought sounds that are unlike the human voice, such as non-continuous impulses with a constant pitch might work well. These are the exact impulses that a percussion instrument delivers. We tested a drum and pads with the EQ and the resulting sounds were very encouraging. We saw near-unlimited possibilities to create any sounds from mere pulse tones using Timbre EQ. We could even make realistic harmonic overtones of traditional instruments referencing physical materials. Further, we had metallic sounds with a disordered harmonic composition. That is, the impulse sounds and Timbre EQ had unexpectedly excellent synergy.”
——— So, it was percussion instruments that produce sounds that suit Timbre EQ.
Arakawa “Exactly. While being simple, percussion instruments can deliver many kinds of impulses depending on the striking technique. This is a great characteristic that is very compatible with Timbre EQ.”
Muroi “To tell the truth, it was EQ, not an instrument, at the very beginning of the development. When we met to exchange various ideas, Ikutaro Kakehashi (Executive Chairman of ATV) suddenly said; ‘Isn’t it more interesting to process sounds picked up by microphones?’ That was actually the starting point of where the aFrame is now. I know he is a specialist in sound processing; even now he sometimes says that many more things could have been done for synthesizers through original sound processing at the time of analog-digital conversion! So, Arakawa took charge of further research on this 'something more interesting with sound processing' about two years ago.”
Arakawa “After that, I explored that 'something interesting,' which is accomplished by splitting the original sounds into spectra and using a filtering algorithm etc. Then, Mr. Ikutaro Kakehashi said to me, ‘Wouldn't it be great if we can have something like Timbre EQ that allows for a change in tone timbres just by operating a knob?’ That is not an EQ that can only change frequency, Q, and the gain of sounds, but an EQ that can also radically change the entire tone timbre. Well, I thought Timbre EQ was so interesting that we began a process of trial and error.”
——— By what algorithm did you try to make “Timbre EQ”?
Arakawa “After a variety of experiments, we noticed that modifying the harmonic makeup can produce interesting sounds; for instance, we superimposed even-harmonic overtones over odd-harmonic overtones. Of course we can’t add any sound component that doesn't exist in the original sound, but any subtlety found in original sound can be amplified. At first we tested by using simple waveforms such as rectangular and sawtooth waves, but these simple waveforms could be transformed into totally different waveforms by modifying the harmonic makeup. We found this interesting and decided to take our R&D efforts down this path.
Next we tested using a human voice as an input source, but the result was really boring! This was because with the human voice the pitch is constantly varying, so equalizing such sounds requires frequencies to follow such variations. However, the pitch has been changed once an input sound is detected. So, the output sounds were unimpressive. Also, with continuous sounds, such as the human voice, variations made by EQ are necessarily masked and the resultant sounds appear to have changed in frequency characteristics only. I presented the sounds to Mr. Ikutaro Kakehashi and as expected, he said ‘That’s no good!’ (Laughs) So, we thought sounds that are unlike the human voice, such as non-continuous impulses with a constant pitch might work well. These are the exact impulses that a percussion instrument delivers. We tested a drum and pads with the EQ and the resulting sounds were very encouraging. We saw near-unlimited possibilities to create any sounds from mere pulse tones using Timbre EQ. We could even make realistic harmonic overtones of traditional instruments referencing physical materials. Further, we had metallic sounds with a disordered harmonic composition. That is, the impulse sounds and Timbre EQ had unexpectedly excellent synergy.”
——— So, it was percussion instruments that produce sounds that suit Timbre EQ.
Arakawa “Exactly. While being simple, percussion instruments can deliver many kinds of impulses depending on the striking technique. This is a great characteristic that is very compatible with Timbre EQ.”

——— I saw the aFrame’s demo movie and I found it very interesting that sound variations by Timbre EQ even followed subtle playing techniques, such as friction on the striking surface. It can produce complex expressions that are not practical with traditional electronic percussion instruments that only trigger PCM sound sources!
Muroi “There is still a significant gap between electronic percussion instruments and acoustic instruments. Existing electronic instruments deliver sounds by triggering PCM sound sources in response to strikes on pads, and this fundamental mechanism has remained virtually unchanged. For PCM sound sources, there is still room for further improvements in realistic tone expressions corresponding to striking intensity and position, as we did with the aD5; however there are various other playing techniques for percussion instruments that are played with hands which cannot be reproduced effectively by the PCM sound source triggering mechanism. Therefore, the idea was to create a new electronic instrument that supports a diverse expression of techniques by processing acoustic sounds by DSP; we would like to marry state-of-the-art digital technologies with an organic feeling. The outcome of such efforts is the aFrame and we refer to this instrument as ‘electrorganic percussion.’”
Kakehashi “What I felt when I tried aFrame for the first time was ‘Hey, it delivers sounds just as expected!’ Although the sounds are electronic, I can control them quite intuitively. I had never experienced this sense of unity and expression with any other electronic instrument.”
Arakawa “Ikuo looked so impressed, and said, ‘The sound feel is impressive! It goes way beyond existing electronic percussion!’ Yes, but it was nothing special for us, the developers, because we know that it just picked up the sounds by microphones and equalized them (Laughs). Of course, there is no latency.”
Muroi “There is still a significant gap between electronic percussion instruments and acoustic instruments. Existing electronic instruments deliver sounds by triggering PCM sound sources in response to strikes on pads, and this fundamental mechanism has remained virtually unchanged. For PCM sound sources, there is still room for further improvements in realistic tone expressions corresponding to striking intensity and position, as we did with the aD5; however there are various other playing techniques for percussion instruments that are played with hands which cannot be reproduced effectively by the PCM sound source triggering mechanism. Therefore, the idea was to create a new electronic instrument that supports a diverse expression of techniques by processing acoustic sounds by DSP; we would like to marry state-of-the-art digital technologies with an organic feeling. The outcome of such efforts is the aFrame and we refer to this instrument as ‘electrorganic percussion.’”
Kakehashi “What I felt when I tried aFrame for the first time was ‘Hey, it delivers sounds just as expected!’ Although the sounds are electronic, I can control them quite intuitively. I had never experienced this sense of unity and expression with any other electronic instrument.”
Arakawa “Ikuo looked so impressed, and said, ‘The sound feel is impressive! It goes way beyond existing electronic percussion!’ Yes, but it was nothing special for us, the developers, because we know that it just picked up the sounds by microphones and equalized them (Laughs). Of course, there is no latency.”
Beautiful bamboo frame hand-crafted by experienced craftsmen
——— I think you must have considered various possible shapes and materials for a percussion instrument equipped with Timbre EQ. What made you decide on this style?
Arakawa “There were twists and turns. As for the shape, we thought that a round shape like a snare drum would be nice, but it produced less variation in sounds, lacking the expressive capacity.”
Muroi “The aFrame is not just a controller. The sounds produced by it are critical. So we paid a lot of attention to its shape and materials. With a round shape it would never get beyond Bessel function effects, so we made corners, because a shape with corners can deliver the sounds of totally different harmonic composition, depending on where a player strikes it.”
Kakehashi “This means complex sounds work well with Timbre EQ, rather than ordered sounds.”
Arakawa “There were twists and turns. As for the shape, we thought that a round shape like a snare drum would be nice, but it produced less variation in sounds, lacking the expressive capacity.”
Muroi “The aFrame is not just a controller. The sounds produced by it are critical. So we paid a lot of attention to its shape and materials. With a round shape it would never get beyond Bessel function effects, so we made corners, because a shape with corners can deliver the sounds of totally different harmonic composition, depending on where a player strikes it.”
Kakehashi “This means complex sounds work well with Timbre EQ, rather than ordered sounds.”
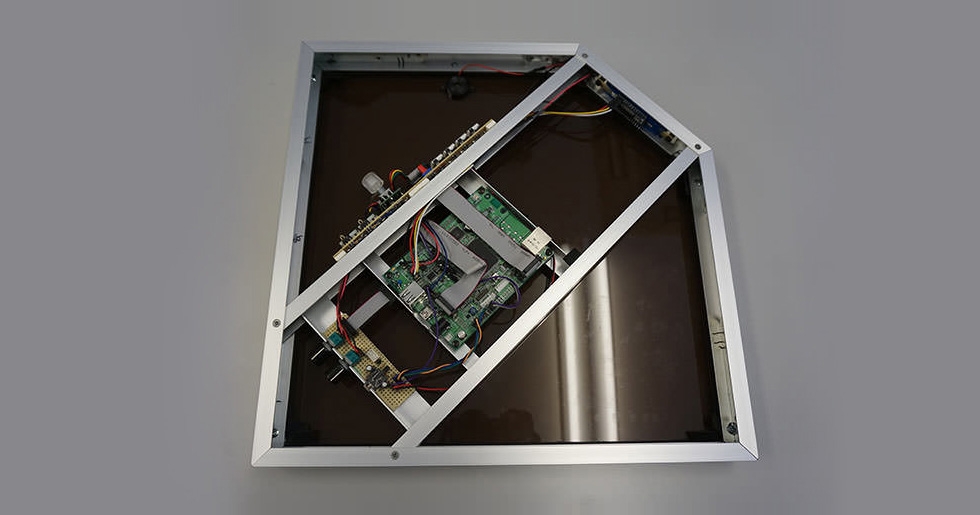
——— OK, you decided on the shape in that way. So what about the size?
Arakawa “It was Ikutaro Kakehashi’s call (Laughs). When I asked him, ‘What size do you think it should be?’ he instantly answered, ‘38cm!’”
Muroi “38cm is a perfect size. Portability might be impaired if it is any larger and it could limit playing styles if any smaller.”
——— It is not a simple square form; it is a unique diamond shape with one corner trimmed.
Kakehashi “A corner is cut off to give it an iconic design. It looks asymmetric with the trimmed corner placed to the right or left, or it can be symmetric if it is held in the middle. We thought it would be interesting to see different looks depending on how a player holds it. Also, a shape with one edge trimmed perfectly fits into a generic snare drum stand, although this is not what we were going for.”
Muroi “Also, coincidentally, it means 'cutting-edge instrument' (Laughs).”
Kakehashi “(Laughs) Yes, and it also means 'Kakehashi' (phonetically this means 'trimmed edge' in Japanese).”
Arakawa “It was Ikutaro Kakehashi’s call (Laughs). When I asked him, ‘What size do you think it should be?’ he instantly answered, ‘38cm!’”
Muroi “38cm is a perfect size. Portability might be impaired if it is any larger and it could limit playing styles if any smaller.”
——— It is not a simple square form; it is a unique diamond shape with one corner trimmed.
Kakehashi “A corner is cut off to give it an iconic design. It looks asymmetric with the trimmed corner placed to the right or left, or it can be symmetric if it is held in the middle. We thought it would be interesting to see different looks depending on how a player holds it. Also, a shape with one edge trimmed perfectly fits into a generic snare drum stand, although this is not what we were going for.”
Muroi “Also, coincidentally, it means 'cutting-edge instrument' (Laughs).”
Kakehashi “(Laughs) Yes, and it also means 'Kakehashi' (phonetically this means 'trimmed edge' in Japanese).”
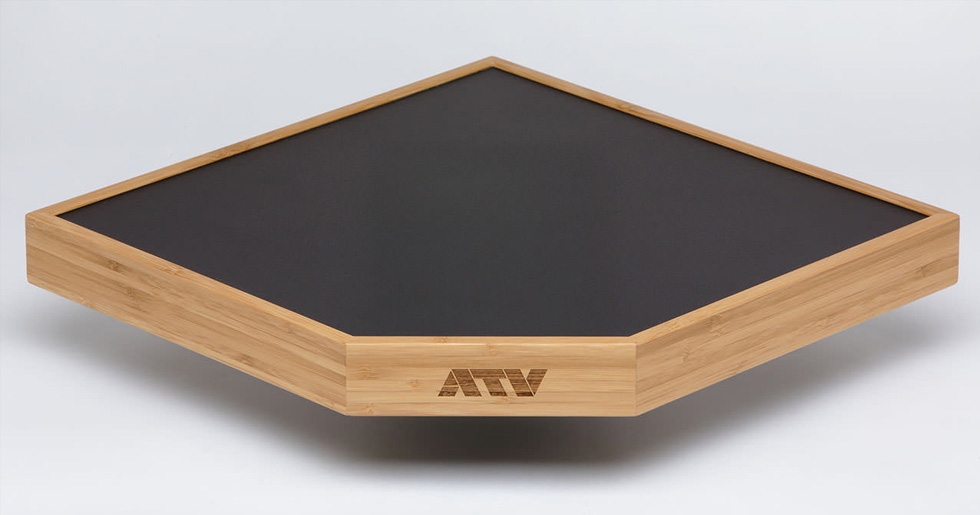
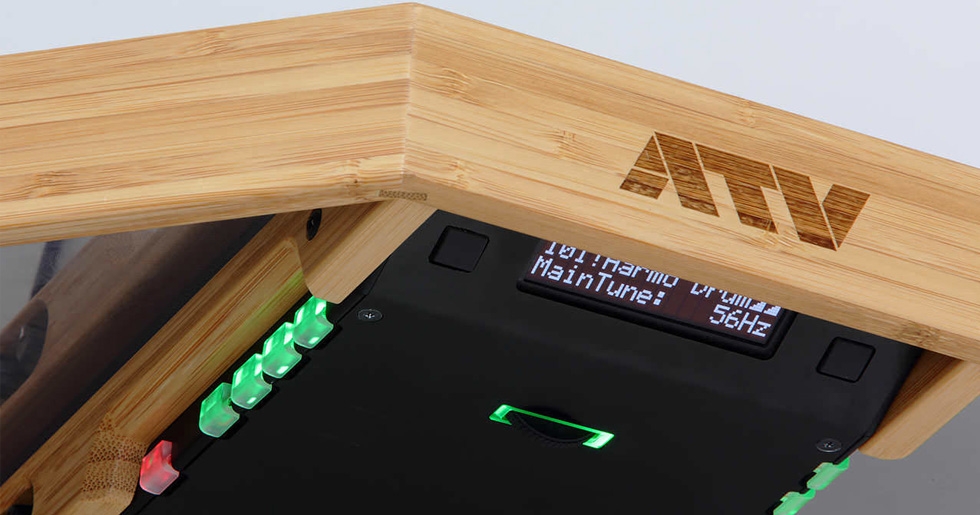
——— What about the percussion surface material?
Tanaka “It’s polycarbonate. Acrylic boards were first used for prototypes, but we concluded it should be more rigid.”
Kakehashi “What is good about polycarbonate is its elasticity. Also, I feel it produce low-pitched tones more effectively than other materials.”
Tanaka “The rough surface texture of this polycarbonate is also nice.”
Kakehashi “We used a slick material at first, but later we noticed the rough surface gives better performance expression.”
——— I was surprised that the frame part is made of laminated bamboo!
Arakawa “The metallic materials we tried first also produced good tones, but we wanted to use wood because the aFrame is an instrument, not a controller.”
Kakehashi “A metal frame makes it look like just a gadget. I wanted an instrument, not a gadget.”
Arakawa “So, we started to search for the best wood for aFrame, and Ikuo said, ‘What about bamboo?’ At that time I thought, ‘Bamboo? He's just blurting out all of his strange thoughts as usual!’ and I let it pass (Laughs).”
Kakehashi “I visited my friend’s newly-built house about 10 years ago and its floors were made of bamboo. The feel of the bamboo underfoot was so nice that it left an impression on me. That’s why I thought bamboo would suit the concept of the aFrame.”
Arakawa “Yet, I never thought we could use bamboo as a frame material, and so I consulted specialists at a factory about it.”
——— So you contacted a music instrument factory?
Arakawa “Yes. We naturally decided to contact Fujigen, because it has a long-standing relationship with Ikutaro Kakehashi and has a factory in the same area, Matsumoto. Above all, their woodcraft techniques are superb. So, Tanaka contacted Fujigen.”
Tanaka “Fujigen has many factories and I wasn’t sure which factory I should contact. So I contacted them via their website (Laughs). I explained the concept of aFrame and asked for consultation in person.”
Arakawa “We then brought a prototype aFrame to them, that was last November.”
——— (To Fujigen representatives) What was the first impression you had then?
Komatsu (Mr. Kei Komatsu, Director and Manager of Manufacturing Dept., CA Business Unit, Fujigen, Inc.) “I remember that we were very interested in the concept of an unprecedented music instrument. When I actually heard the sounds, I thought, ‘That’s great! I want it!’ (Laughs) So my first impression was: ‘We would like to make this instrument!’”
Furuya (Mr. Eiji Furuya, Director and CA Business Unit Manager, Fujigen, Inc.) “Also, Mr. Ikutaro Kakehashi was an old friend of the late Yoshimochi Kamijo, the former president, so it was our pleasure to work with ATV again.”
——— What kind of materials did Fujigen propose first?
Komatsu “As we have produced a wide variety of wooden components for electric guitars, I thought we should recommend mahogany, ash or something like that. However, they asked ‘Can you make the frame of bamboo?’”
Arakawa “Because Ikuo suggested bamboo, I thought it wouldn’t hurt to ask (Laughs). But they actually said, ‘Yes,’ and brought a laminated bamboo sample from their back lot!”
——— What instruments have you used bamboo for?
Komatsu “We had never used it for music instruments (Laughs). The laminated bamboo sample was for an automotive part.”
Furuya “It was not until two or three years ago that bamboo started to attract attention. I’m not sure about the reason, but there have been a number of inquiries about bamboo in relation to automotive parts and we started to use laminated bamboo materials in last a few years.”
Arakawa “We finally received a prototype with a laminated bamboo frame. When I first saw it, I was amazed at its quality feel. It was far more than I expected. It sounded nice even without powering up, and I thought it is already an instrument as is. It became the only choice for us. We decided to make the aFrame with bamboo.”
Tanaka “It’s polycarbonate. Acrylic boards were first used for prototypes, but we concluded it should be more rigid.”
Kakehashi “What is good about polycarbonate is its elasticity. Also, I feel it produce low-pitched tones more effectively than other materials.”
Tanaka “The rough surface texture of this polycarbonate is also nice.”
Kakehashi “We used a slick material at first, but later we noticed the rough surface gives better performance expression.”
——— I was surprised that the frame part is made of laminated bamboo!
Arakawa “The metallic materials we tried first also produced good tones, but we wanted to use wood because the aFrame is an instrument, not a controller.”
Kakehashi “A metal frame makes it look like just a gadget. I wanted an instrument, not a gadget.”
Arakawa “So, we started to search for the best wood for aFrame, and Ikuo said, ‘What about bamboo?’ At that time I thought, ‘Bamboo? He's just blurting out all of his strange thoughts as usual!’ and I let it pass (Laughs).”
Kakehashi “I visited my friend’s newly-built house about 10 years ago and its floors were made of bamboo. The feel of the bamboo underfoot was so nice that it left an impression on me. That’s why I thought bamboo would suit the concept of the aFrame.”
Arakawa “Yet, I never thought we could use bamboo as a frame material, and so I consulted specialists at a factory about it.”
——— So you contacted a music instrument factory?
Arakawa “Yes. We naturally decided to contact Fujigen, because it has a long-standing relationship with Ikutaro Kakehashi and has a factory in the same area, Matsumoto. Above all, their woodcraft techniques are superb. So, Tanaka contacted Fujigen.”
Tanaka “Fujigen has many factories and I wasn’t sure which factory I should contact. So I contacted them via their website (Laughs). I explained the concept of aFrame and asked for consultation in person.”
Arakawa “We then brought a prototype aFrame to them, that was last November.”
——— (To Fujigen representatives) What was the first impression you had then?
Komatsu (Mr. Kei Komatsu, Director and Manager of Manufacturing Dept., CA Business Unit, Fujigen, Inc.) “I remember that we were very interested in the concept of an unprecedented music instrument. When I actually heard the sounds, I thought, ‘That’s great! I want it!’ (Laughs) So my first impression was: ‘We would like to make this instrument!’”
Furuya (Mr. Eiji Furuya, Director and CA Business Unit Manager, Fujigen, Inc.) “Also, Mr. Ikutaro Kakehashi was an old friend of the late Yoshimochi Kamijo, the former president, so it was our pleasure to work with ATV again.”
——— What kind of materials did Fujigen propose first?
Komatsu “As we have produced a wide variety of wooden components for electric guitars, I thought we should recommend mahogany, ash or something like that. However, they asked ‘Can you make the frame of bamboo?’”
Arakawa “Because Ikuo suggested bamboo, I thought it wouldn’t hurt to ask (Laughs). But they actually said, ‘Yes,’ and brought a laminated bamboo sample from their back lot!”
——— What instruments have you used bamboo for?
Komatsu “We had never used it for music instruments (Laughs). The laminated bamboo sample was for an automotive part.”
Furuya “It was not until two or three years ago that bamboo started to attract attention. I’m not sure about the reason, but there have been a number of inquiries about bamboo in relation to automotive parts and we started to use laminated bamboo materials in last a few years.”
Arakawa “We finally received a prototype with a laminated bamboo frame. When I first saw it, I was amazed at its quality feel. It was far more than I expected. It sounded nice even without powering up, and I thought it is already an instrument as is. It became the only choice for us. We decided to make the aFrame with bamboo.”
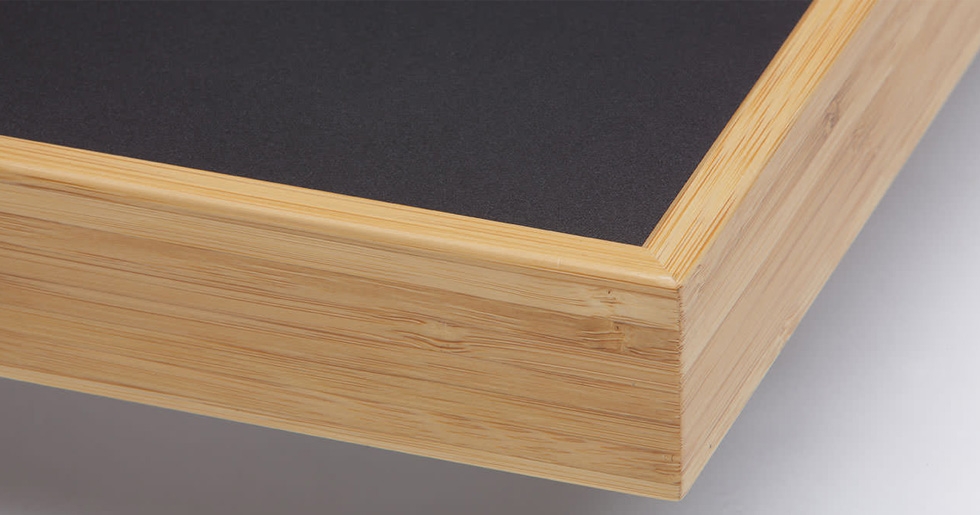
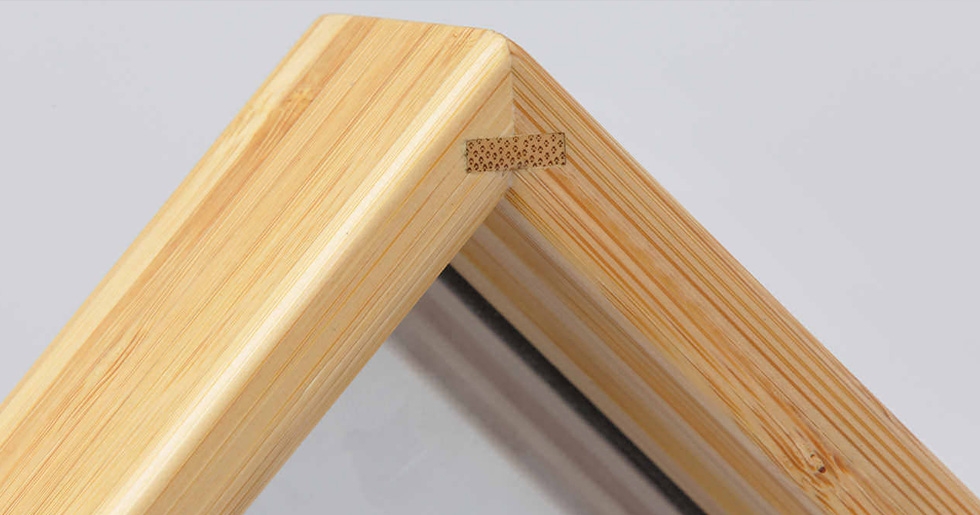
——— What are the primary characteristics of bamboo in comparison with mahogany and ash?
Ono (Mr. Kazutaka Ono, CA Business Unit, Fujigen, Inc.) “It’s light and sturdy. It’s not as light as ash, but it’s very hard.”
Furuya “There is also the benefit of a less chance of deformation with bamboo. Further, bamboo is constantly available and will never go out-of-stock; this is an important factor in material selection for mass-produced products. More importantly, bamboo is a symbolic material of traditional Japanese products.”
——— I saw it with my own eyes, and I noticed the details, such as the seams between bamboo panels are very sophisticated in construction.
Furuya “To joint multiple bamboo blocks, we make a spline called a hozo on each block and bond them with a key joint called a yatoizane between them. This is a traditional Japanese craftsman technique that uses no nails or screws.”
Ono “A yatoizane requires professional craftsmanship as it cannot be mated by machines, even if a highly precise computer-controlled machine is used. Of course, we automate various other tasks for volume production, but professional craftsmanship cannot be omitted in finishing if quality products are to be made.”
Furuya “Precise work and bonding are necessary to provide strength. That is what we have learned from our long history of music instrument making.”
——— What about the surface finishing?
Furuya “Matte-satin finishing, combined with a bamboo-specific silky texture, provides an excellent feeling on the hands.”
——— The commercial release version will have a Fujigen brand stamp on it.
Furuya “Yes, this will be proof that it is 'Made in Azumino' (Laughs). In this factory, we mostly create handmade instruments, including musical boxes, but we wanted to create other kinds of instruments, too. So, it was a wonderful coincidence that ATV contacted us last year. It was our great pleasure to produce such an innovative instrument in Azumino.”
Ono (Mr. Kazutaka Ono, CA Business Unit, Fujigen, Inc.) “It’s light and sturdy. It’s not as light as ash, but it’s very hard.”
Furuya “There is also the benefit of a less chance of deformation with bamboo. Further, bamboo is constantly available and will never go out-of-stock; this is an important factor in material selection for mass-produced products. More importantly, bamboo is a symbolic material of traditional Japanese products.”
——— I saw it with my own eyes, and I noticed the details, such as the seams between bamboo panels are very sophisticated in construction.
Furuya “To joint multiple bamboo blocks, we make a spline called a hozo on each block and bond them with a key joint called a yatoizane between them. This is a traditional Japanese craftsman technique that uses no nails or screws.”
Ono “A yatoizane requires professional craftsmanship as it cannot be mated by machines, even if a highly precise computer-controlled machine is used. Of course, we automate various other tasks for volume production, but professional craftsmanship cannot be omitted in finishing if quality products are to be made.”
Furuya “Precise work and bonding are necessary to provide strength. That is what we have learned from our long history of music instrument making.”
——— What about the surface finishing?
Furuya “Matte-satin finishing, combined with a bamboo-specific silky texture, provides an excellent feeling on the hands.”
——— The commercial release version will have a Fujigen brand stamp on it.
Furuya “Yes, this will be proof that it is 'Made in Azumino' (Laughs). In this factory, we mostly create handmade instruments, including musical boxes, but we wanted to create other kinds of instruments, too. So, it was a wonderful coincidence that ATV contacted us last year. It was our great pleasure to produce such an innovative instrument in Azumino.”
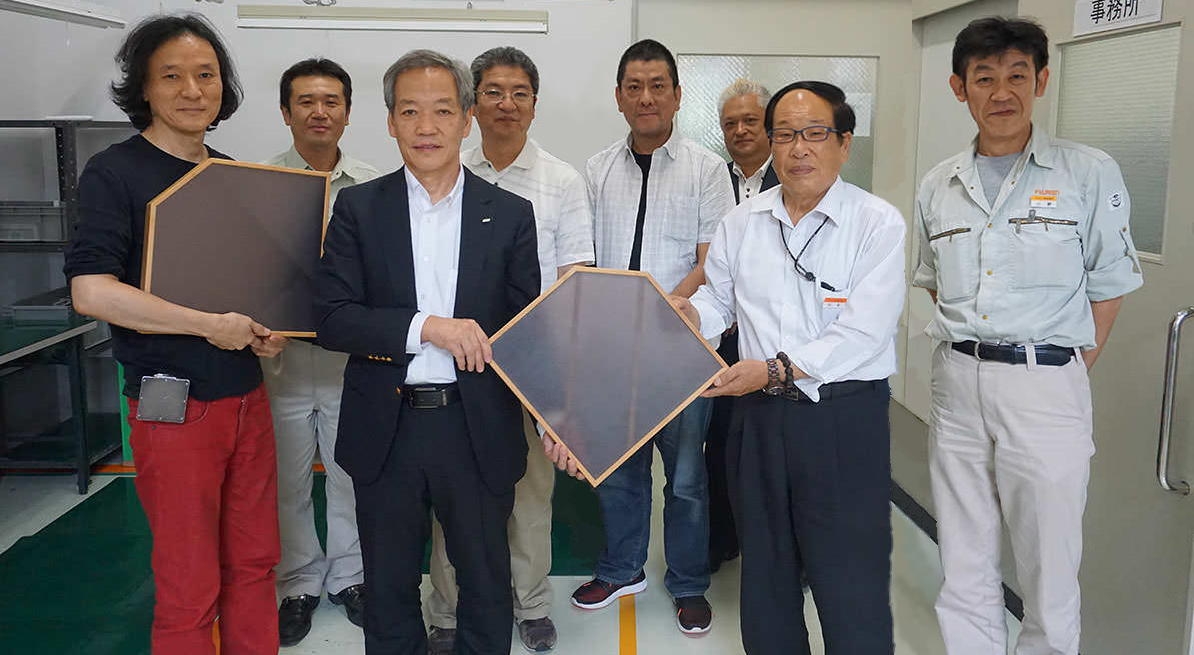
All parameters are open and users can freely produce tones
——— How many microphones are built into it?
Arakawa “There are two general piezo-microphones: one at the edge for high-range tones, and one at the center of the striking surface for low-range tones.”
——— You must have determine the number of microphones very carefully.
Arakawa “Yes, but we decided two would be enough at a very early stage. However, we added a pressure sensor later, as Ikuo requested a muting feature.”
Kakehashi “I requested it because performers would want to stop tones as part of their performance expression techniques; from the performers’ standpoint, a muting feature was a must.”
Arakawa “We first tried to mute sounds by using input sound thresholds but it was horribly unnatural (Laughs). So we decided to simply add a pressure sensor.”
——— That’s why there are two microphone outputs to the processor.
Arakawa “That’s right. The AD/DA converter is 24 bit/48 kHz and the processor is the same as aD5’s, i.e. an ARM Core. Processing is all handled by the ARM Core, so the configuration is quite simple.”
Arakawa “There are two general piezo-microphones: one at the edge for high-range tones, and one at the center of the striking surface for low-range tones.”
——— You must have determine the number of microphones very carefully.
Arakawa “Yes, but we decided two would be enough at a very early stage. However, we added a pressure sensor later, as Ikuo requested a muting feature.”
Kakehashi “I requested it because performers would want to stop tones as part of their performance expression techniques; from the performers’ standpoint, a muting feature was a must.”
Arakawa “We first tried to mute sounds by using input sound thresholds but it was horribly unnatural (Laughs). So we decided to simply add a pressure sensor.”
——— That’s why there are two microphone outputs to the processor.
Arakawa “That’s right. The AD/DA converter is 24 bit/48 kHz and the processor is the same as aD5’s, i.e. an ARM Core. Processing is all handled by the ARM Core, so the configuration is quite simple.”
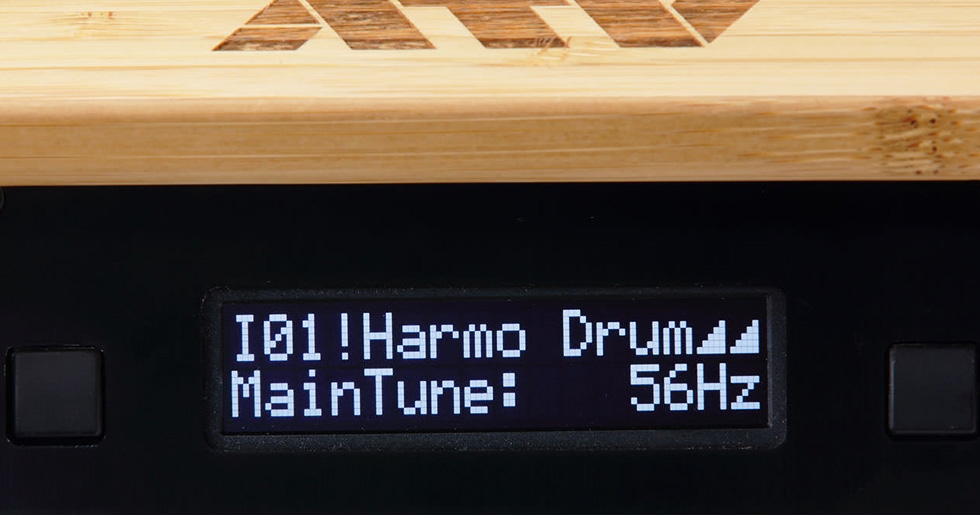
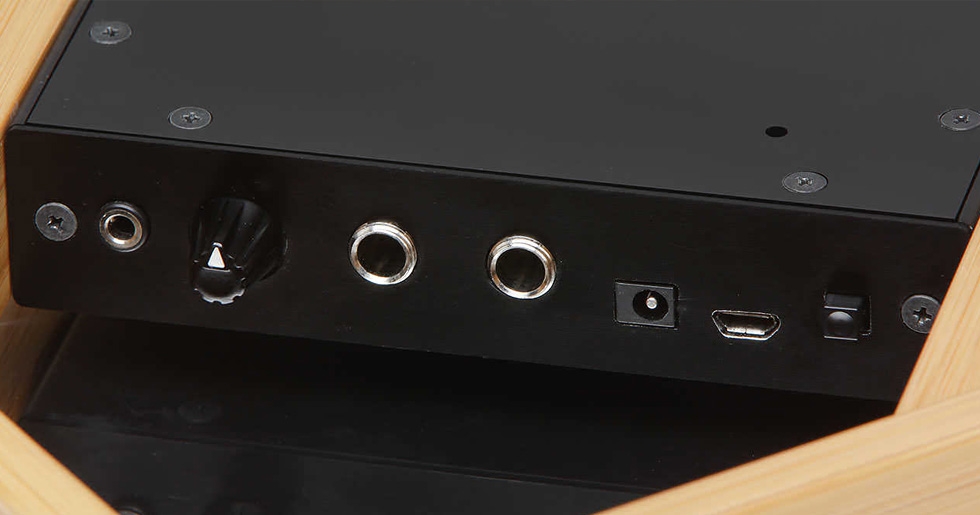
——— Would you explain more about the Timbre EQ mechanism that creates aFrame's tones?
Arakawa “The details are confidential, but I can say that there are three Timbre EQ units in the aFrame to modify the harmonic makeup of input sounds: a main timbre primarily for low range, a sub timbre primarily for high range, and an extra timbre for additional sound color. Thanks to the extra timbre, it may create characteristic sounds like the snare sounds of a snare drum or the claps of a beatbox. There is a mixer that consolidates the three Timbre EQ units. There is also delay, phaser, flanger, reverb, and wah-wah effectors downstream.”
——— Are these parameters to be disclosed to users?
Arakawa “Certainly. Users can edit the parameters with the supplied LCD display and encoder. We plan to allow users to do so from PC via a USB connection in the future.”
Kakehashi “But it is a virtue of the aFrame that users can edit the parameters without the need to connect something else. The Encoder is also positioned perfectly so that users can perform editing with one hand while the other hand is playing.”
——— The built-in effectors seem effective, too.
Muroi “For example, it's interesting to change reverb depth by adjusting the pressure. That could also change a players’ playing style.”
Kakehashi “The muting feature is also configurable. Users may even change the subjective strike sensing range without changing the tone characteristics by editing the parameters. It is also good to have the three Timbre EQ units not completely segregated into audio bands; partially-overlapped harmonics can create totally different sounds.”
——— How many factory preset configurations will be available?
Arakawa “There will be 40, and users can save up to 40 other user preset configurations.”
——— Is power supplied through an AC adapter?
Kakehashi “Yes, but an OTC mobile battery can be used as a power source via the USB terminal. You can also connect a wireless transmitter for audio output for a cable free experience. Of course you can use a shoulder strap, too.”
Arakawa “The details are confidential, but I can say that there are three Timbre EQ units in the aFrame to modify the harmonic makeup of input sounds: a main timbre primarily for low range, a sub timbre primarily for high range, and an extra timbre for additional sound color. Thanks to the extra timbre, it may create characteristic sounds like the snare sounds of a snare drum or the claps of a beatbox. There is a mixer that consolidates the three Timbre EQ units. There is also delay, phaser, flanger, reverb, and wah-wah effectors downstream.”
——— Are these parameters to be disclosed to users?
Arakawa “Certainly. Users can edit the parameters with the supplied LCD display and encoder. We plan to allow users to do so from PC via a USB connection in the future.”
Kakehashi “But it is a virtue of the aFrame that users can edit the parameters without the need to connect something else. The Encoder is also positioned perfectly so that users can perform editing with one hand while the other hand is playing.”
——— The built-in effectors seem effective, too.
Muroi “For example, it's interesting to change reverb depth by adjusting the pressure. That could also change a players’ playing style.”
Kakehashi “The muting feature is also configurable. Users may even change the subjective strike sensing range without changing the tone characteristics by editing the parameters. It is also good to have the three Timbre EQ units not completely segregated into audio bands; partially-overlapped harmonics can create totally different sounds.”
——— How many factory preset configurations will be available?
Arakawa “There will be 40, and users can save up to 40 other user preset configurations.”
——— Is power supplied through an AC adapter?
Kakehashi “Yes, but an OTC mobile battery can be used as a power source via the USB terminal. You can also connect a wireless transmitter for audio output for a cable free experience. Of course you can use a shoulder strap, too.”
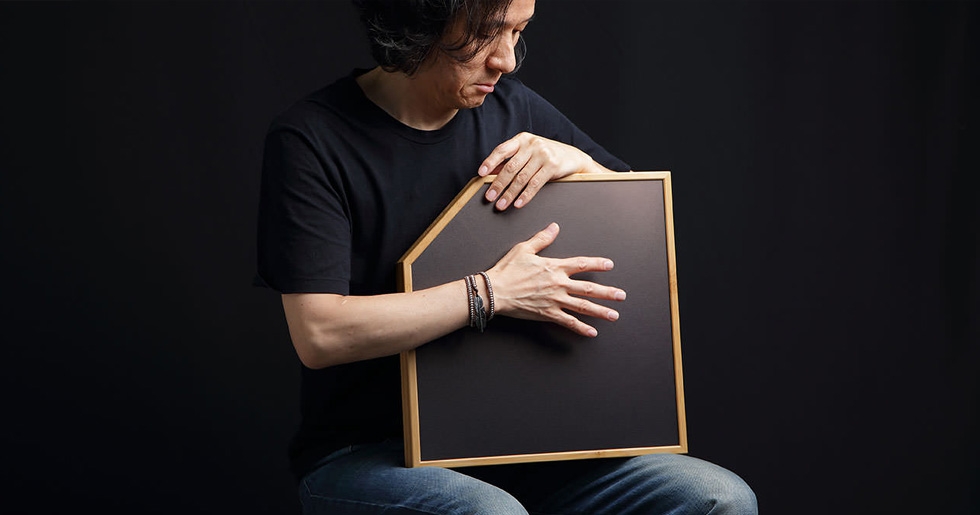
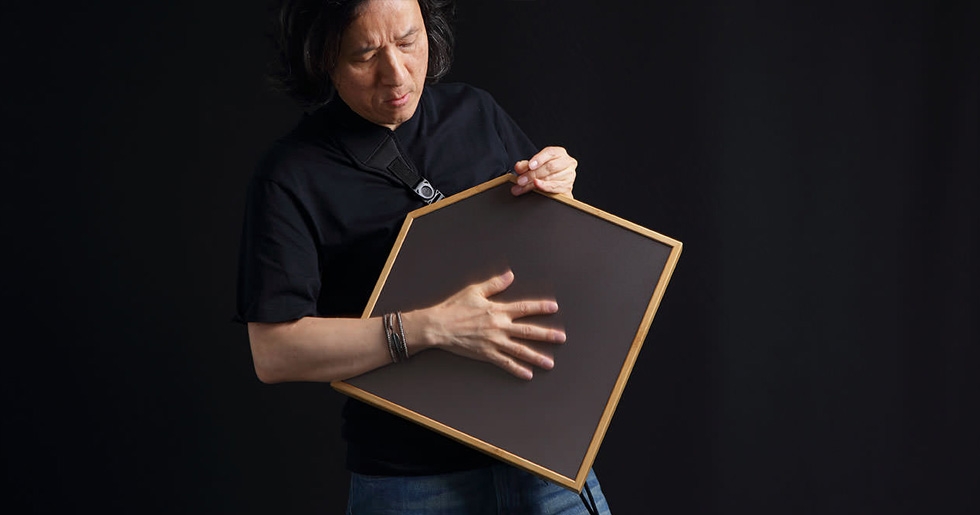
aFrame – an innovative electronic instrument inspiring musicians
——— Can anyone who has ever performed a percussion instrument perform on the aFrame right away?
Kakehashi “You don’t need any experience with percussion instruments, anyone can play it just by striking or rubbing it. It’s a percussion instrument, so you strike it and it makes a sound! Very simple. I hope users will enjoy this freedom in their performance.”
Arakawa “I hope so, too. And I hope they will also enjoy the extra freedom of making sounds. We will disclose all the parameters for users to accomplish this.”
Kakehashi “I think instructions or interventions from our side should be minimal. I believe the player's imagination and instincts will create a better performance and sound.”
Kakehashi “You don’t need any experience with percussion instruments, anyone can play it just by striking or rubbing it. It’s a percussion instrument, so you strike it and it makes a sound! Very simple. I hope users will enjoy this freedom in their performance.”
Arakawa “I hope so, too. And I hope they will also enjoy the extra freedom of making sounds. We will disclose all the parameters for users to accomplish this.”
Kakehashi “I think instructions or interventions from our side should be minimal. I believe the player's imagination and instincts will create a better performance and sound.”
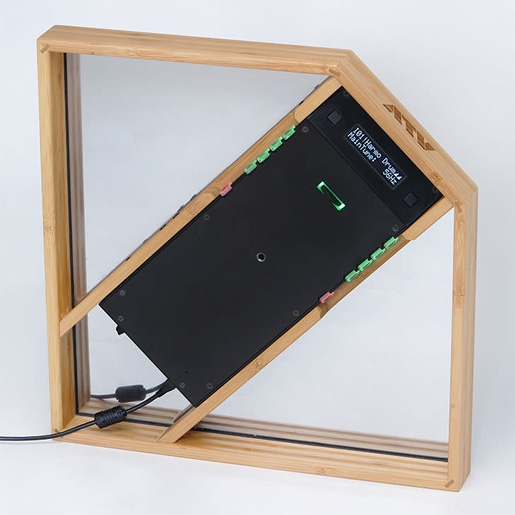
——— What difficulties did you face in the development of the aFrame?
Arakawa “We had a lot of fun, rather than difficulties. For example, it was very pleasing to exchange opinions with professional musicians. I presented prototypes to Ikuo and other performers such as Mr. Motokazu Shinoda and Mr. Tommy Snyder and I got feedback from them, which we used as the basis to improve the product in development, step by step. This kind of process in the making of a new instrument was a lot of fun.”
Muroi “The key was to keep going. If we had given up when we heard the boring sounds made from the human voice in the early phase, we could have never accomplished this.”
Arakawa “Some development team members actually said to us ‘This is boring.’ When we told this to Mr. Ikutaro Kakehashi, he said ‘Don’t worry about it. Let’s do this with people who find it interesting.’ That was so encouraging!”
Tanaka “Personally, I faced many difficulties, but I shouldn‘t talk about those kind of things now, because I could go on forever about that (Laughs).”
——— Mr. Ikuo Kakehashi, what aspects of the aFrame interest you based on your extensive experience playing various percussion instruments?
Kakehashi “There are two factors that are important for us to develop as musicians: who we have played with and what instruments we have played. This is what I’ve felt in doing music for many years. The aFrame offers something inspiring to performers. I find such an inspiring instrument quite attractive, even if it is not yet mature. In contrast, electronic instruments that merely trigger poor quality PCM sound sources in layers only spoil musicians. Also, I feel an attachment to the aFrame as an instrument. I feel like holding it and never letting go (Laughs). It is pleasant to the touch and I love the way it feels in my hands! It is similar to the feeling some have toward the guitar.”
Arakawa “We had a lot of fun, rather than difficulties. For example, it was very pleasing to exchange opinions with professional musicians. I presented prototypes to Ikuo and other performers such as Mr. Motokazu Shinoda and Mr. Tommy Snyder and I got feedback from them, which we used as the basis to improve the product in development, step by step. This kind of process in the making of a new instrument was a lot of fun.”
Muroi “The key was to keep going. If we had given up when we heard the boring sounds made from the human voice in the early phase, we could have never accomplished this.”
Arakawa “Some development team members actually said to us ‘This is boring.’ When we told this to Mr. Ikutaro Kakehashi, he said ‘Don’t worry about it. Let’s do this with people who find it interesting.’ That was so encouraging!”
Tanaka “Personally, I faced many difficulties, but I shouldn‘t talk about those kind of things now, because I could go on forever about that (Laughs).”
——— Mr. Ikuo Kakehashi, what aspects of the aFrame interest you based on your extensive experience playing various percussion instruments?
Kakehashi “There are two factors that are important for us to develop as musicians: who we have played with and what instruments we have played. This is what I’ve felt in doing music for many years. The aFrame offers something inspiring to performers. I find such an inspiring instrument quite attractive, even if it is not yet mature. In contrast, electronic instruments that merely trigger poor quality PCM sound sources in layers only spoil musicians. Also, I feel an attachment to the aFrame as an instrument. I feel like holding it and never letting go (Laughs). It is pleasant to the touch and I love the way it feels in my hands! It is similar to the feeling some have toward the guitar.”
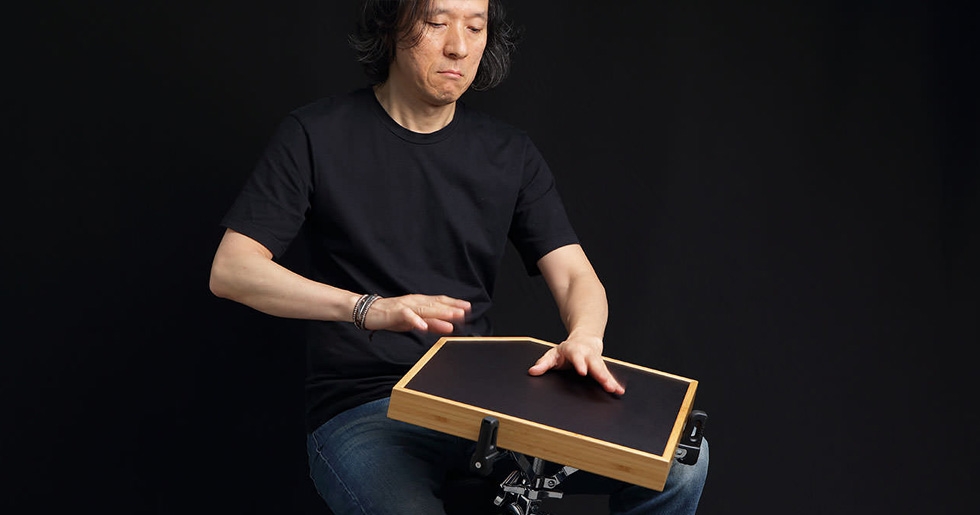
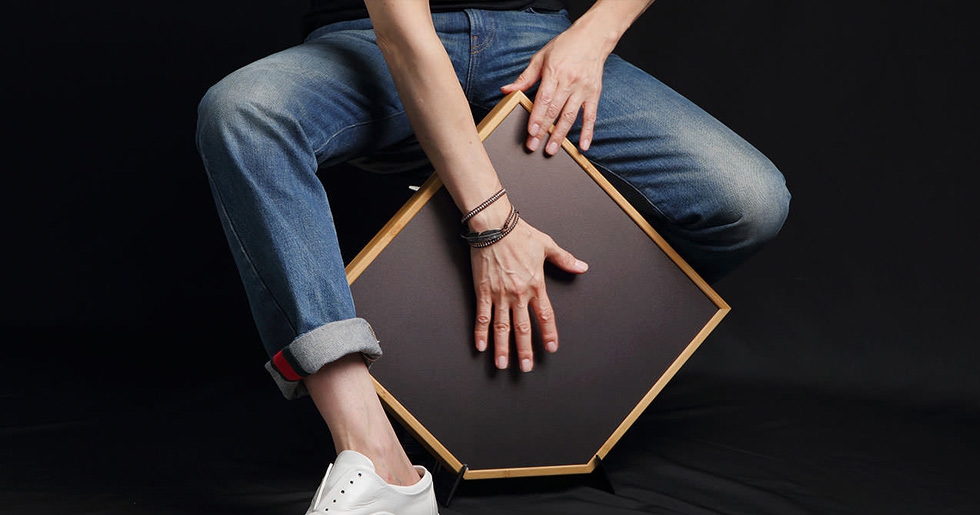
——— I expect the frame part will be beautifully aged through years of use.
Kakehashi “Right, right. Because it is an acoustic instrument with an electronic circuit in it. The balance is really new to us.”
Muroi “From a manufacturer’s perspective, we believe the truly innovative aspect of the aFrame is its ability to produce all these tones and expressions in just this single box. When performing, percussionists traditionally use a variety of instruments at the same time, such congas and bongos. A single aFrame can extend the performance style of such instruments and grant musicians more sonic freedom.”
——— What did Mr. Ikutaro Kakehashi (Executive Chairman) say about aFrame?
Muroi “He is really delighted. Satisfied very much. He suddenly said ‘Let’s do a recital!’ (Laughs)”
Arakawa “The aFrame would have not been born without the idea of Mr. Ikutaro Kakehashi. We did what he said, just as he said, and brought the idea into reality. In fact, the aFrame is a new instrument created by Ikutaro Kakehashi.”
Muroi “For us, the aFrame is a starting point. For the future we see various possibilities in the ‘Adaptive Timbre Technology’ we developed for aFrame. Look forward to ATV’s future products!”
Kakehashi “Right, right. Because it is an acoustic instrument with an electronic circuit in it. The balance is really new to us.”
Muroi “From a manufacturer’s perspective, we believe the truly innovative aspect of the aFrame is its ability to produce all these tones and expressions in just this single box. When performing, percussionists traditionally use a variety of instruments at the same time, such congas and bongos. A single aFrame can extend the performance style of such instruments and grant musicians more sonic freedom.”
——— What did Mr. Ikutaro Kakehashi (Executive Chairman) say about aFrame?
Muroi “He is really delighted. Satisfied very much. He suddenly said ‘Let’s do a recital!’ (Laughs)”
Arakawa “The aFrame would have not been born without the idea of Mr. Ikutaro Kakehashi. We did what he said, just as he said, and brought the idea into reality. In fact, the aFrame is a new instrument created by Ikutaro Kakehashi.”
Muroi “For us, the aFrame is a starting point. For the future we see various possibilities in the ‘Adaptive Timbre Technology’ we developed for aFrame. Look forward to ATV’s future products!”
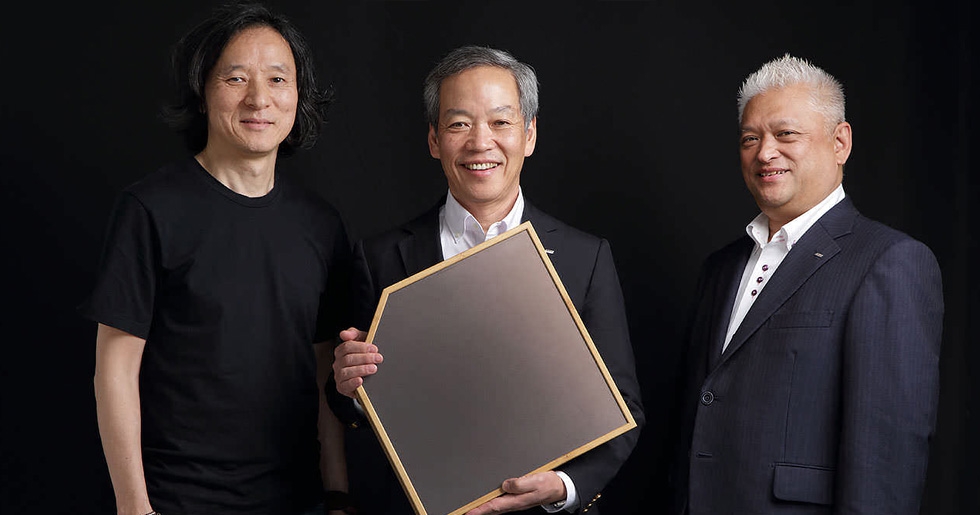